Technical audit / rehabilitation project
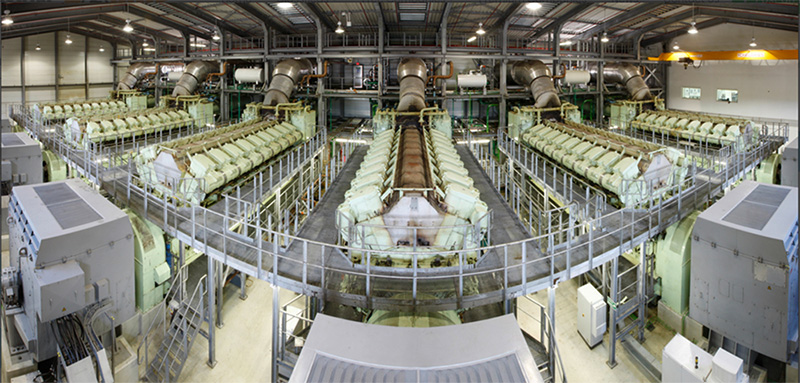
A technology more than a century old, the Diesel engine no longer holds any secrets for marine or Power plant operators or for repairers wherever they are in the world….
So why so many breakdowns, damages, breakages and economic disasters?
At ADR, we put our Engine knowledge and our field experience of the 4-stroke Diesel engine at the service of our Customers in 4 phases:
- Preventive: breakdown is not inevitable
- Diagnosis: identification of the problem, causes and consequences
- Curative: There is no ready-made answer in Diesel repair
- Post-traumatic: Analysis and advice to avoid recurrence
Complex rehabilitation projects ↗
ADR has been deeply involved in complex rehabilitation projects since its creation. This is the center of its service activity and the environment in which its specialists can best express their know-how and skills.
The care given to your projects ↗
ADR also knows what will make the difference between a technically successful complex project and a successful project, we must always keep this difference in mind and take away the modesty that is required.
The reality on the ground ↗
ADR also knows that in the world of industrial engines and despite the care taken, major failure is a condition that cannot be completely ruled out, even if in all modesty, we do our best to ensure that the probability and occurrence are as low as possible.
Our support process
Assistance request
Always different in their forms and origins, detailed or succinct, assistance requests are the necessary tool to identify the need, define the mission and allow us to assign a specialized profile to an intervention.
It is also an important entry point to discuss the planned duration and ensure that the means implemented will correspond to the desired objectives.
Arrival on site – discussion with the contacts
All sites are different in their operation, their history, their operators, the context and ultimately, the problem they encounter.
Arriving on site is a key moment when the operator takes the dimension of the problem in its diversity and can in a few exchanges validate the preparation made on the basis of the information communicated or face a completely different situation.
The strength of ADR operators is knowing how to make a quick analysis of the context to focus on the essentials and best respond to needs whether they are expressed or not.
Check for malfunctions
Whether it is assistance following a breakdown or during maintenance, expertise is a guiding thread where collecting information is the fundamental step in resolving problems.
Questions that are sometimes confusing for the interlocutor but so important for our understanding.
On the scale of the installation and well beyond the engine, even when the latter is the center of the action.
Frankness is an asset so do not be offended when we ask if the engine has been restarted.
Search for causes
Whether the intervention is the result of a malfunction or during scheduled maintenance, it is rare that a wear or breakage problem is organized around a single cause.
The cause tree is aptly named – not forgetting anything is our mission and our commitment.
Propose remedies
At ADR, once the diagnosis has been established, we consider remedies at 2 levels, firstly curative treatment, secondly long-term work:
Of course, firstly, what scope, what programme, what impact on the duration of the intervention, what financial impact, is the proposed repair definitive or temporary and what technical means specific to this discovery will be necessary.
Where a repairer stops …
ADR considers that understanding the mechanisms is the best remedy and to do this, it will continue its assistance approach by becoming a force for proposals to prevent the situation from recurring: maintenance monitoring, training, adaptation of installations to their environment, and above all, the establishment of routines and basic rules.